
“Y-axis straightness travel of less than 10 arcseconds was required, and Makino was the only builder that immediately responded that this wouldn’t be a problem,” he recalls. Whereas most HMCs use a vertical spindle on a horizontal plane, this model features a slant-column structure for a stronger Y axis that resists Z-direction cutting forces, Mr. In assembly, the yoke must hold better than 1 arcsecond per inch of travel. Two of the yoke’s most critical features, a pair of identical bores located on opposite ends of the part, require bore accuracies of ±5 microns and location tolerances of ☒.5 microns. QVI began its search for a solution by evaluating HMCs from several manufacturers based on the specific design and engineering requirements of the 302’s yoke, which moves in one axis and carries the sensors that move on it in a perpendicular axis (the third axis moves across the base). “Also, while profitable machining for us once meant utilizing machine tools long after they were paid for, the 302 required capabilities that could be found only in modern, high-performance machining centers.” “Most machine tools require a sacrifice in accuracy for a larger work envelope, which we couldn’t afford,” Mr. High production goals and the size of these parts, which necessitated a larger machine, further compounded the problem. The shop soon found that meeting the tight tolerances required for the base plate and X-axis yoke was much more difficult in aluminum than the hardened, ground tool steel with which it was more accustomed to working. “A key to manufacturing the 302 was a high strength-to-weight ratio,” Mr. Aluminum comprises 90 percent of its weight. With a 300- by 300- by 250-mm measuring volume, the SmartScope Flash 302 is the largest benchtop machine in OGP’s inventory.

“That’s why we manufacture base-model components here in Rochester.”Ī few years ago, two critical components for one particular multi-sensor system, the base plate and X-axis yoke, proved difficult to machine to specification. “The sensors work throughout the system’s usable volume, so overall accuracy depends on the base-model construction,” explains David Wolf, QVI shopfloor manager. In addition to providing extremely detailed measurements, such systems can inspect more part dimensions in a single setup than their more dedicated counterparts, the company says. Starting with a selection of 50 standard models, the company can also engineer customized measurement solutions for specific customer applications.įor its part, OGP focuses on multi-sensor systems, which often include lasers, touch probes, microprobes and other sensor types that work in conjunction with video measurement technology. Through these brands, the company offers a diverse product range covering a wide spectrum of industries. Two HMCs from Makino (Mason, Ohio) not only provided the precision needed to produce these parts, but also significantly reduced cycle times.ĭigital Tools Meet Practical Applicationsįounded in 1945 in Rochester, New York, QVI is a worldwide supplier of metrology equipment marketed under various brands, including OGP, VIEW Micro-Metrology, Quality Vision Services, RAM Optical Instrumentation and Certified Comparator Products. A few years ago, however, the tight tolerances and high production requirements of components for one multi-sensor measuring system exceeded the capabilities of the shop’s manufacturing equipment.
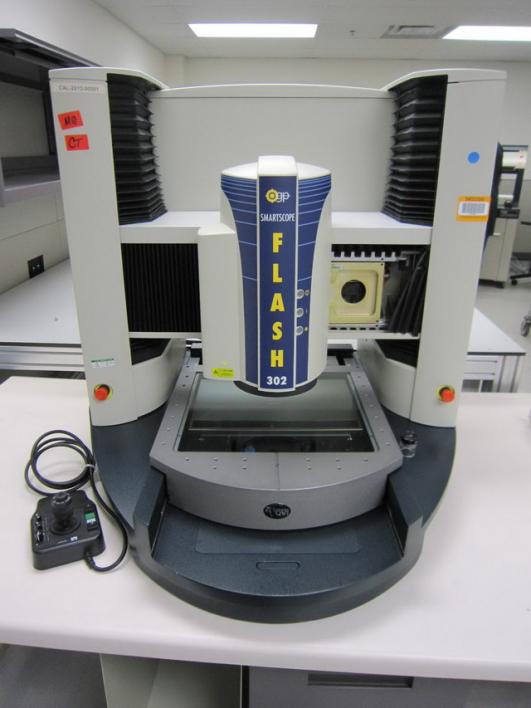
QVI contracts some work out to manufacturing partners, but the company produces the most critical components at its in-house machine shop to control quality and accuracy. “We’re fighting the same battle as our customers-always improving accuracy and manufacturing methods so we can deliver superior products,” says Stephen Flynn, president of measurement and inspection equipment supplier Optical Gaging Products (OGP), a division of Quality Vision International (QVI). In order to deliver the requisite precision, that metrology equipment often must be manufactured to standards that are even more stringent than those of the parts it measures. Manufacturers of precision-engineered, high-end products require sophisticated metrology equipment for effective quality control.
